CUSTOMIZATION
ONE-STOP PERSONALIZED SOLUTION
We provide pharmaceutical automation equipment software and hardware customization options to fully meet your needs for commercial retail smart devices.
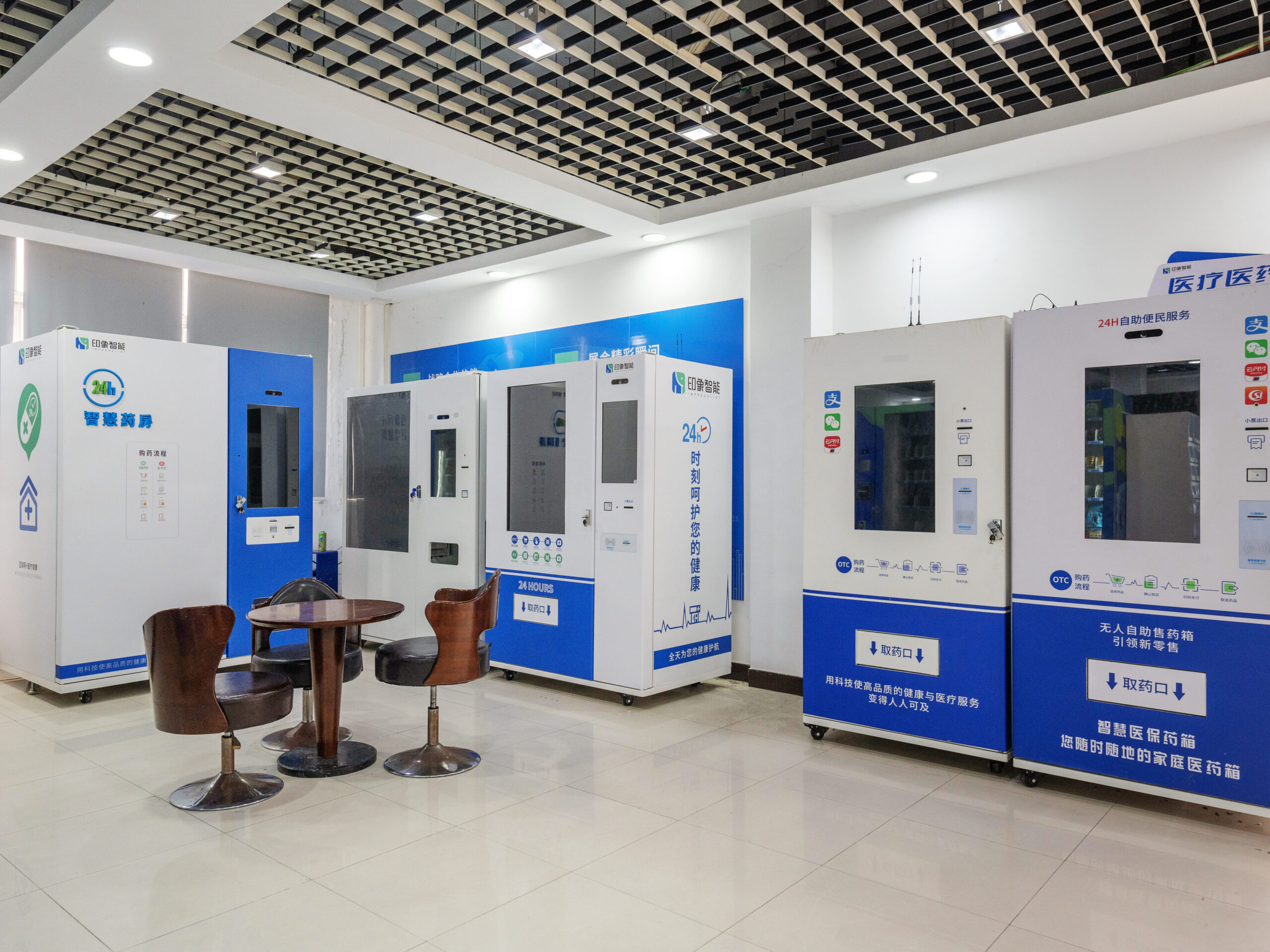
without quantity requirements
Whether you need a single or multiple vending machines, we can provide you with thoughtful and comprehensive customization services.
support ODM and OEM
We have a professional team of software and hardware engineers to meet your various customization needs and support ODM and OEM services.
Rich production experience
We have been deeply involved in the automatic new retail industry for ten years, accumulated rich industry experience, and focused on ensuring the product quality .
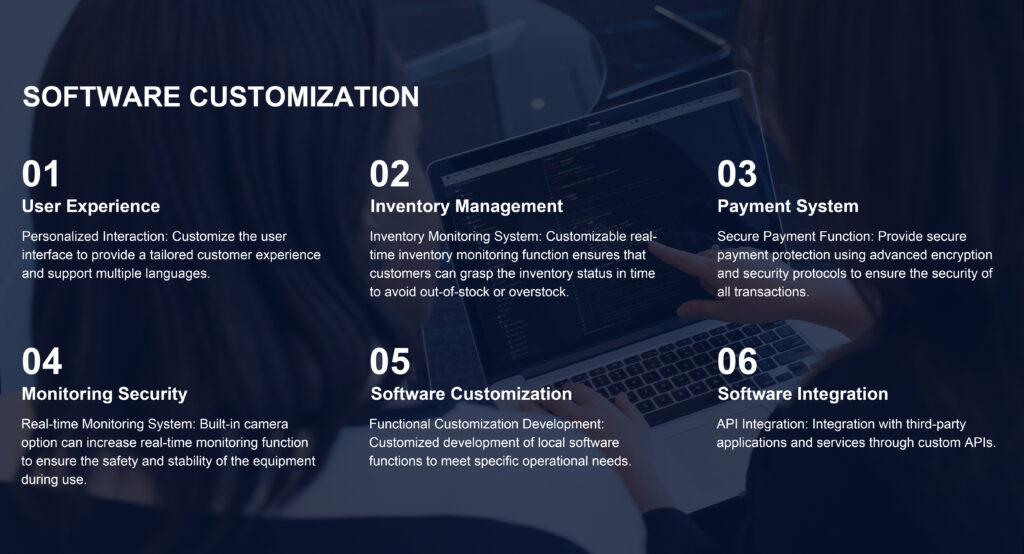
HARDWARE CUSTOMIZATION
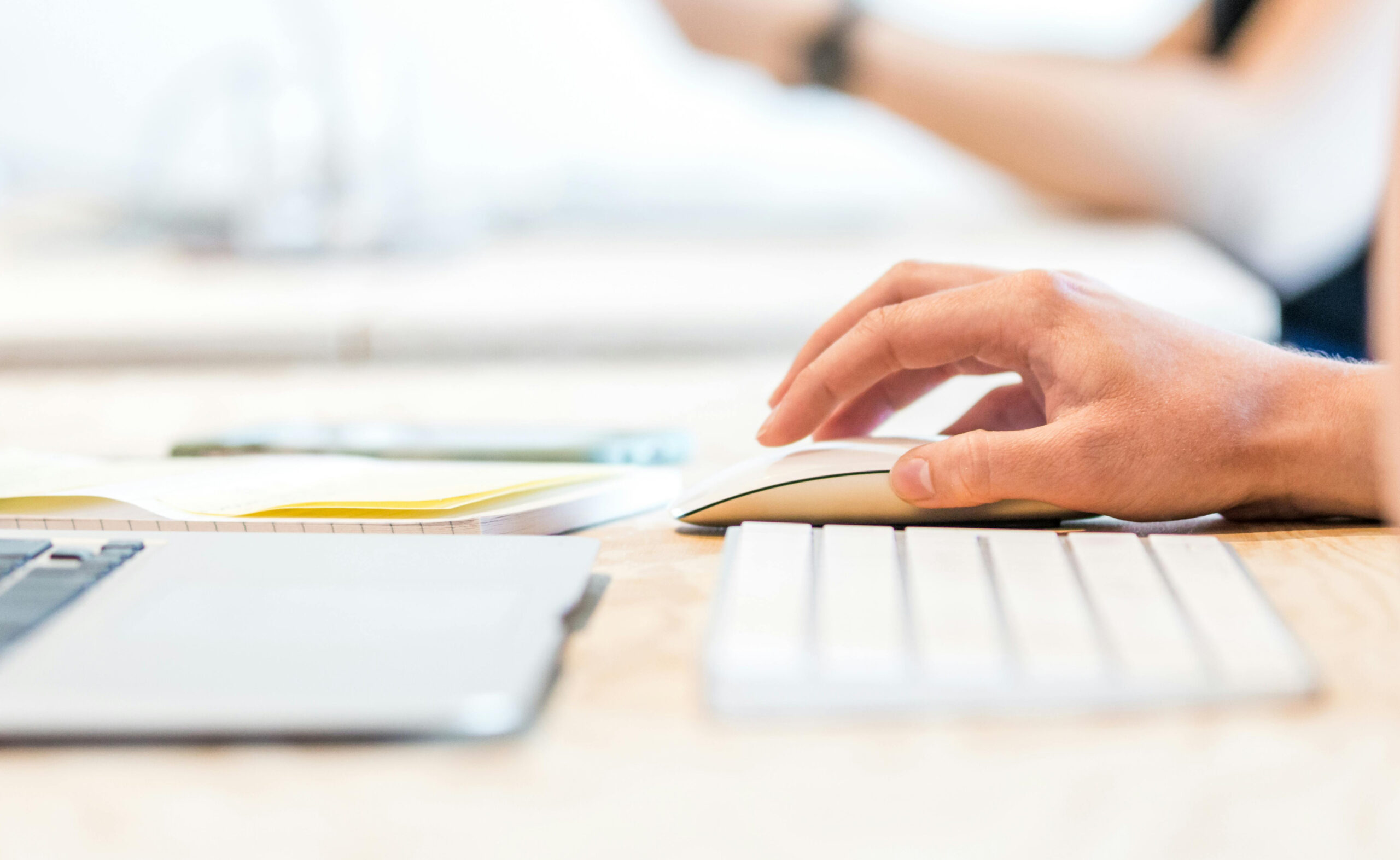
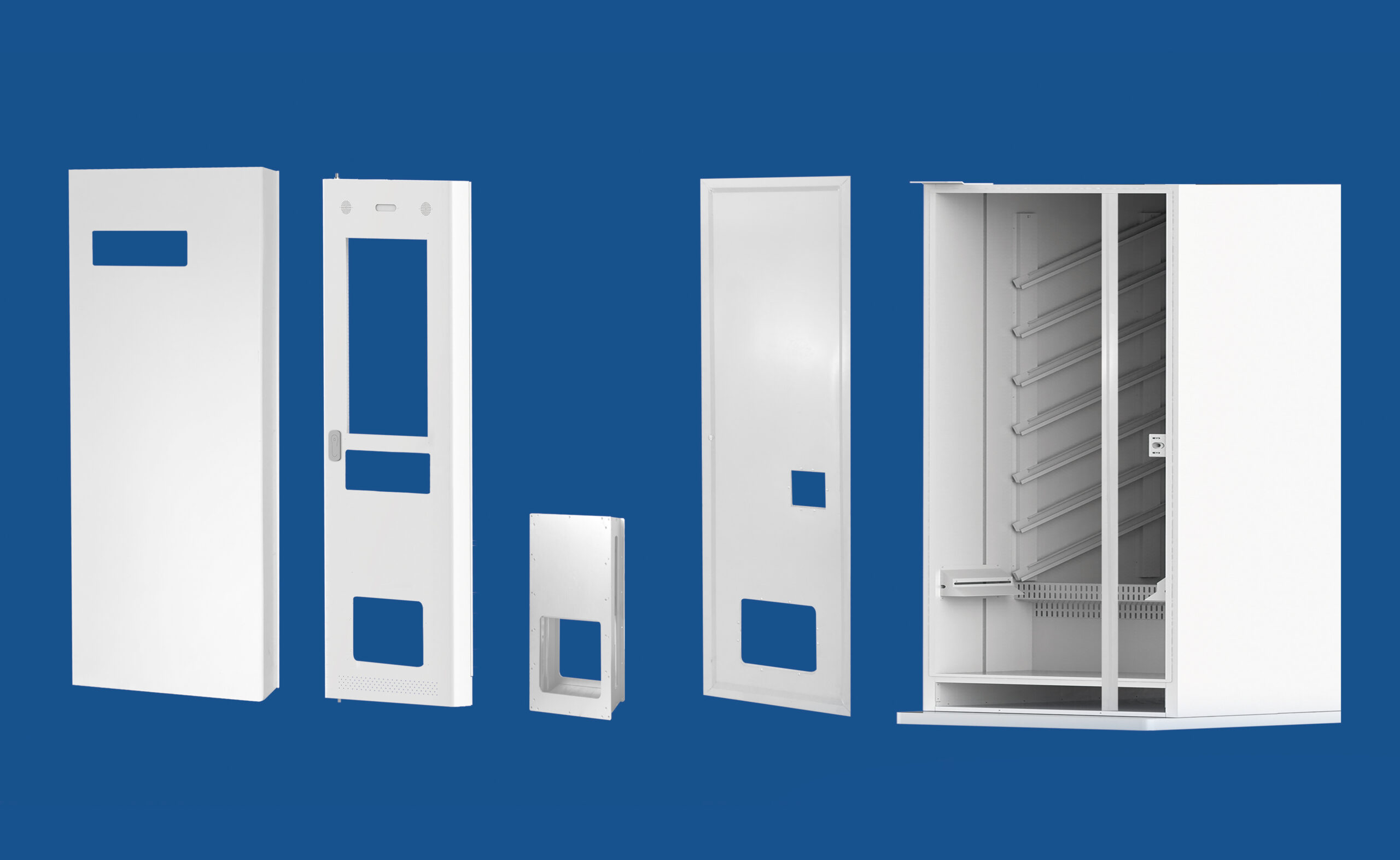
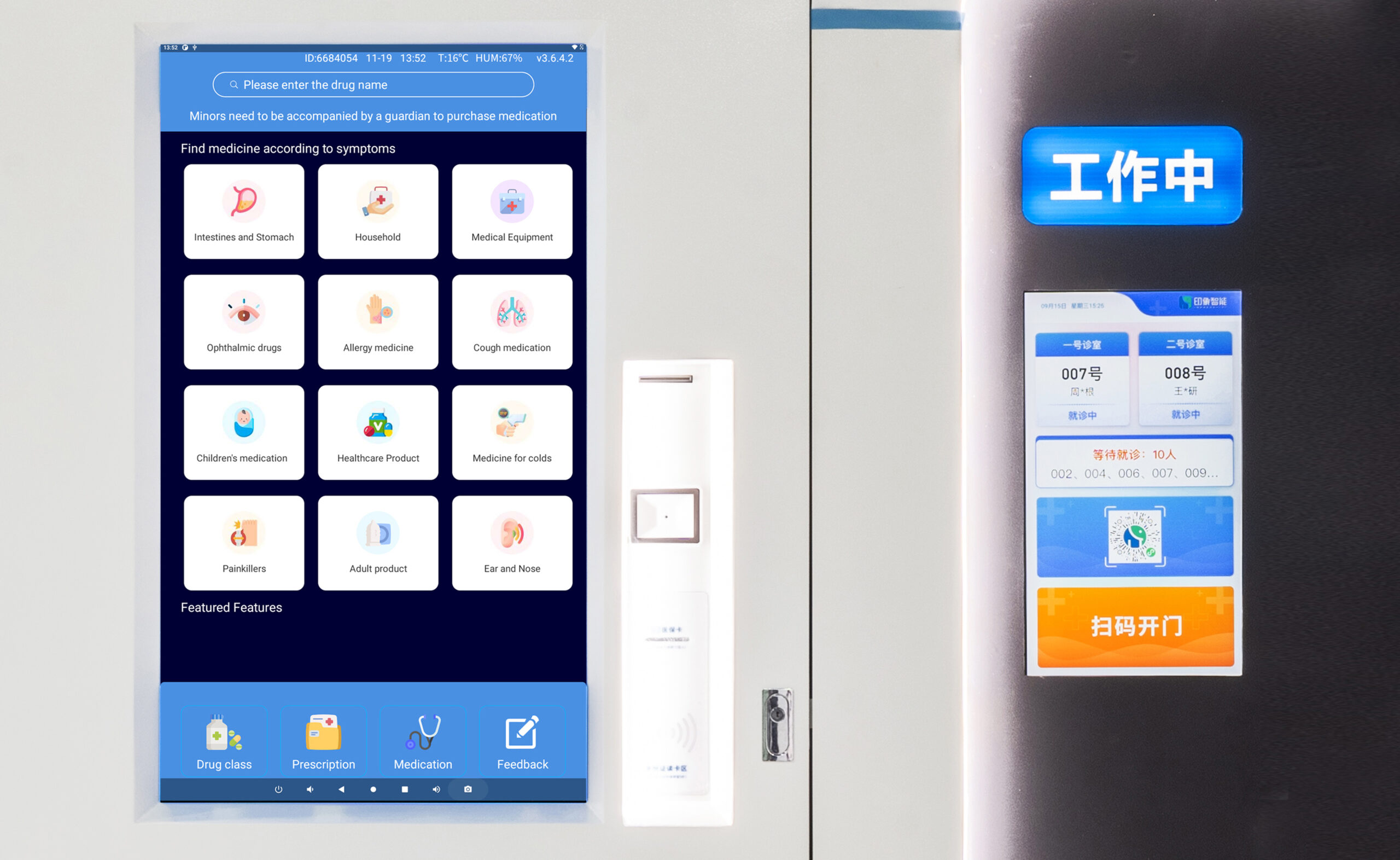
Appearance design
Color selection: A variety of color options are available, and customers can choose the right color according to their brand image and market demand.
Material selection
Casing material: According to the equipment use environment and aesthetic requirements, customers can choose different casing materials, such as stainless steel, plastic, or alloy.
Product Display
Screen display: You can customize touch screens of various sizes or choose our standard 21.5-inch and 43-inch screens.
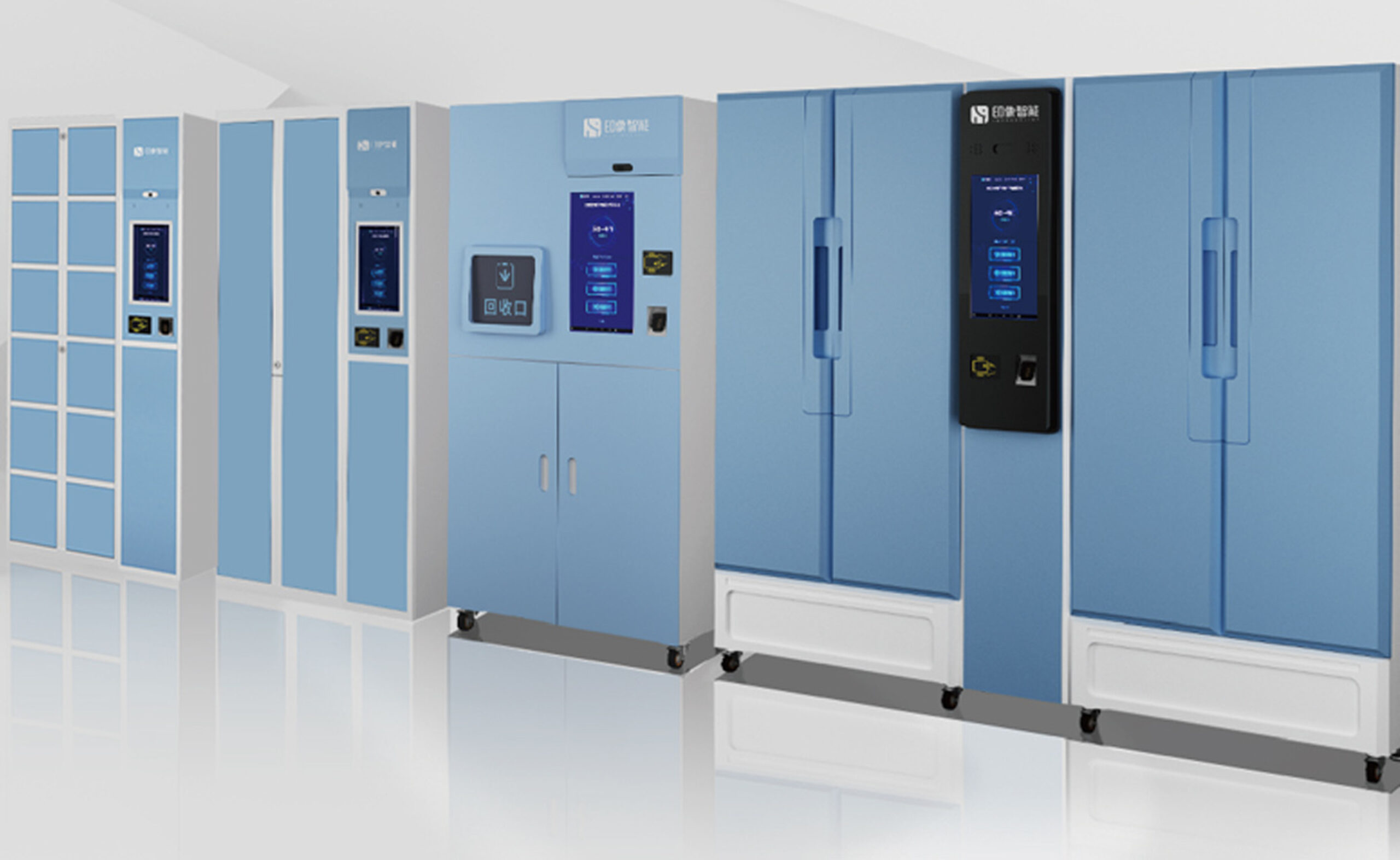
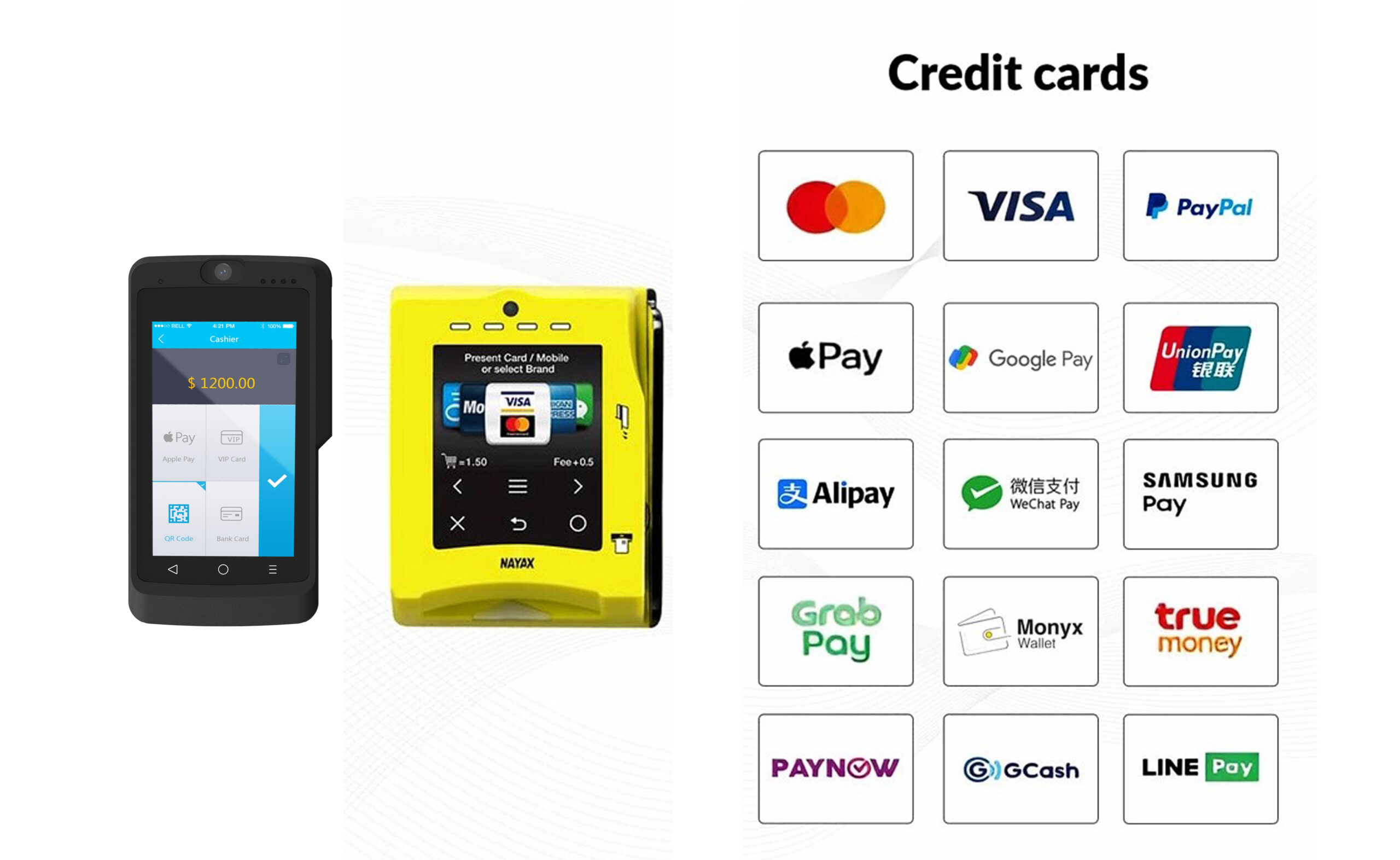
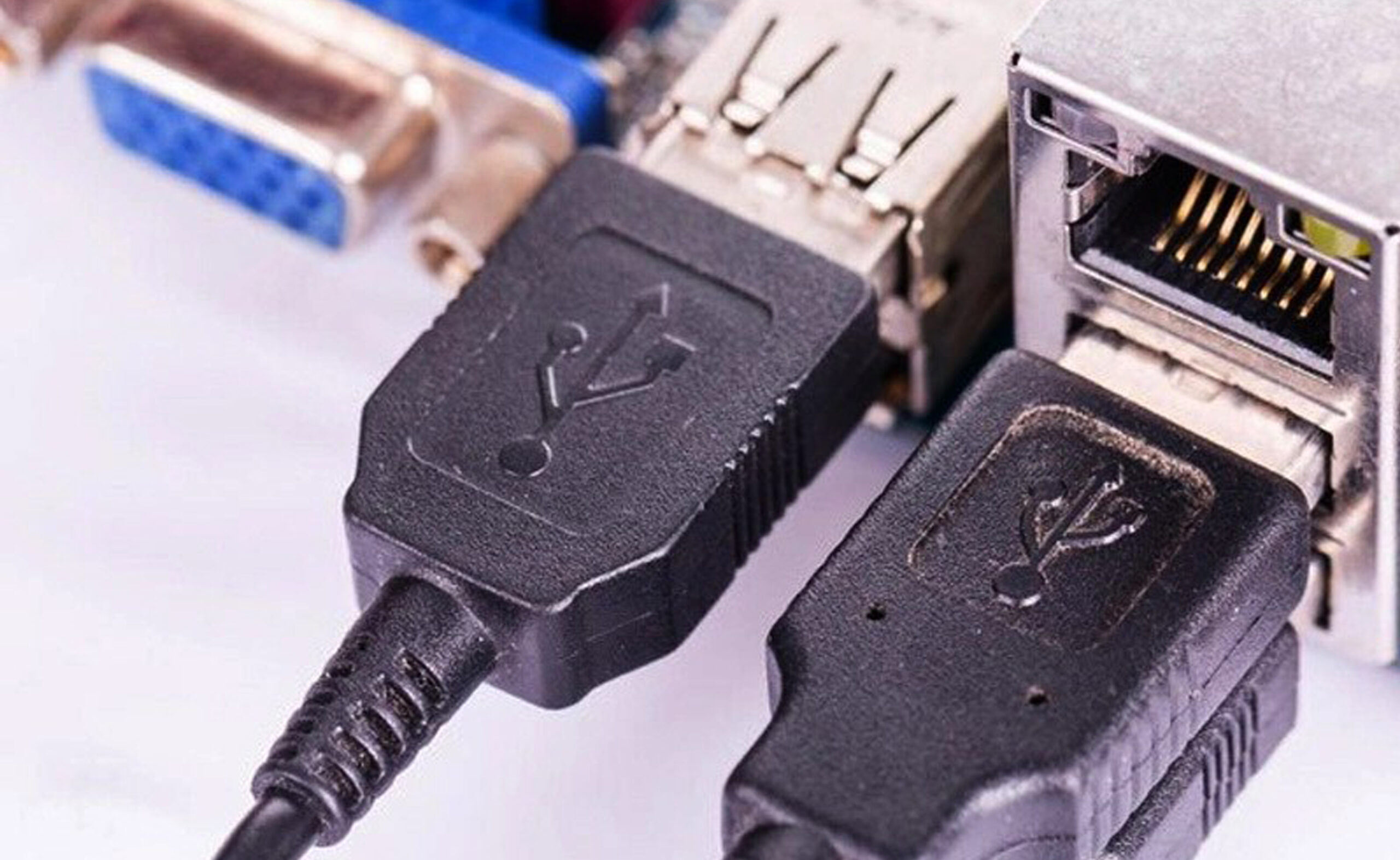
Size and shape
Size adjustment: According to the customer’s space requirements, the overall size of the device can be customized to ensure that it adapts to the specific place of use.
Payment function
Payment function: cash payment (traditional coin and banknote acceptors), card payment (credit and debit card readers), mobile payment, Age recognition (intelligent age recognition card reader), etc.
Compatibility design
Power adapter: Customize the power adapter solution according to the voltage and frequency of the region to ensure the normal use of the device in different markets.
pharmaceutical automation equipment CUSTOMIZATION PROCESS
IMT provides full-process customization services, from demand analysis to production delivery, ensuring that each project perfectly meets customer needs.
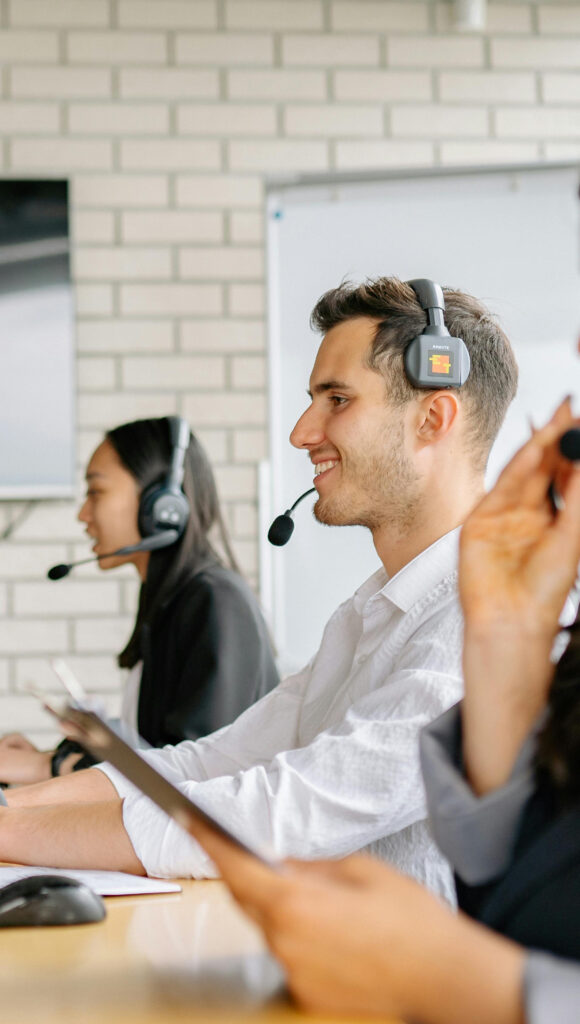
01. Demand communication
Customers can contact our sales team by phone, email, or online consultation. We will arrange for professional consultants to have one-on-one, in-depth communication with you to learn more about your specific needs, budget, expected functions, design style, etc.
02. Solution design
After fully understanding customer needs, our designers will proceed to develop a preliminary design plan, including hardware appearance, functional configuration and software interface. we will provide customers with sketches or 3D models so that customers can intuitively understand the final effect.
03. Confirm the plan
We’ll discuss the preliminary design with customers, collect feedback, and adjust as needed. Upon customer confirmation, we’ll develop a detailed plan including production schedule and delivery date, for customer approval.
04. Manufacturing
Per the approved design plan, we’ll perform regular in-process checks to ensure quality compliance at each stage. Post-production, preliminary functional tests will verify full equipment functionality.
05. Test Verification
After the equipment is manufactured, we will conduct a comprehensive quality inspection and performance verification ,including the evaluation of the safety, stability, and service life of the equipment to ensure that it can perform well in actual operation.
06. Delivery and Installation
After testing, we’ll deliver the equipment to the customer’s location. Upon arrival, our technical team will remotely guide installation and commissioning to ensure operation and provide training on procedures.
07. Subsequent Support
After the equipment is installed, we will continue to provide technical support to customers, answer any questions during operation, and solve problems that may arise during use.